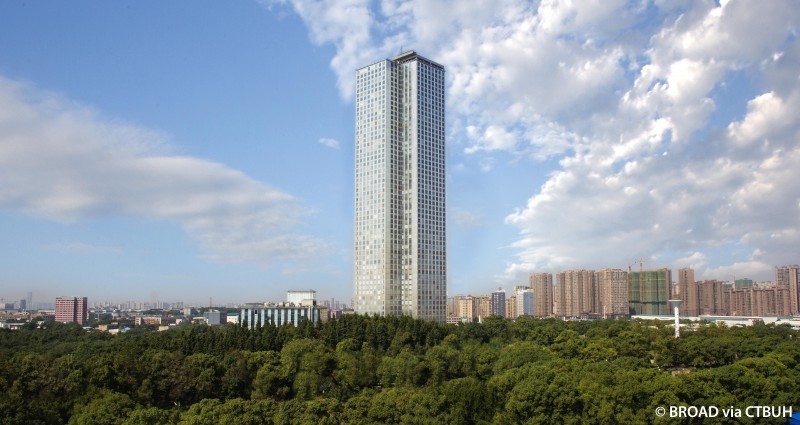
The Mini Sky City – How architects built a 57-story skyscraper in just 19 days
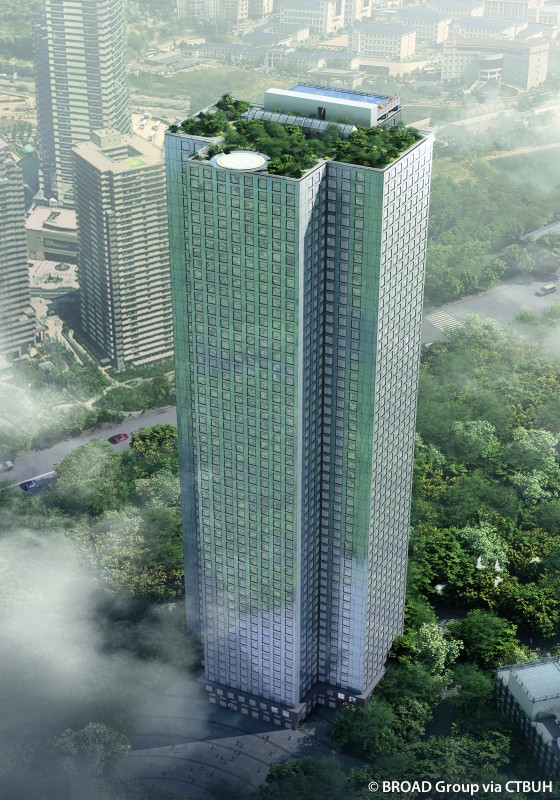
In Changsha, China, one of the fastest built buildings is making history. The Broad Sustainable Building Co. – a prefab construction firm – managed to erect a 57-story skyscraper in just 19 working days. This shocking feat was discussed worldwide and took up top headlines in sites like The Guardian and New York Post. Continue reading to find out how a construction company managed to achieve this.
What was the secret?
The secret was modular construction. Noted by Xiao Changgeng – the vice-president of the Broad Sustainable Building Co. – the company put up the rectangular, glass and steel Mini Sky City, assembling three floors a day, using a modular method. “With the traditional method, they have to build a skyscraper brick by brick, but with our method, we just need to assemble the blocks,” company engineer Chen Xiangqian said in an interview with New York Post. Such approach to building and construction are famous for high-rise apartment blocks elsewhere as well, including Britain and the U.S. Some critics even believe that the method could lead to cityscapes with overly uniform architecture. But what is modular construction and how does it work?
Modular construction – what is it?
Modular construction, also known as prefabricated or off-site construction, is a construction method where buildings are constructed and manufactured in sections or modules off-site using controlled plant conditions before being transported and assembled at a final location. In short terms, it is factory-made components that are assembled on-site. These modules are typically designed to fit together seamlessly to create a complete building.
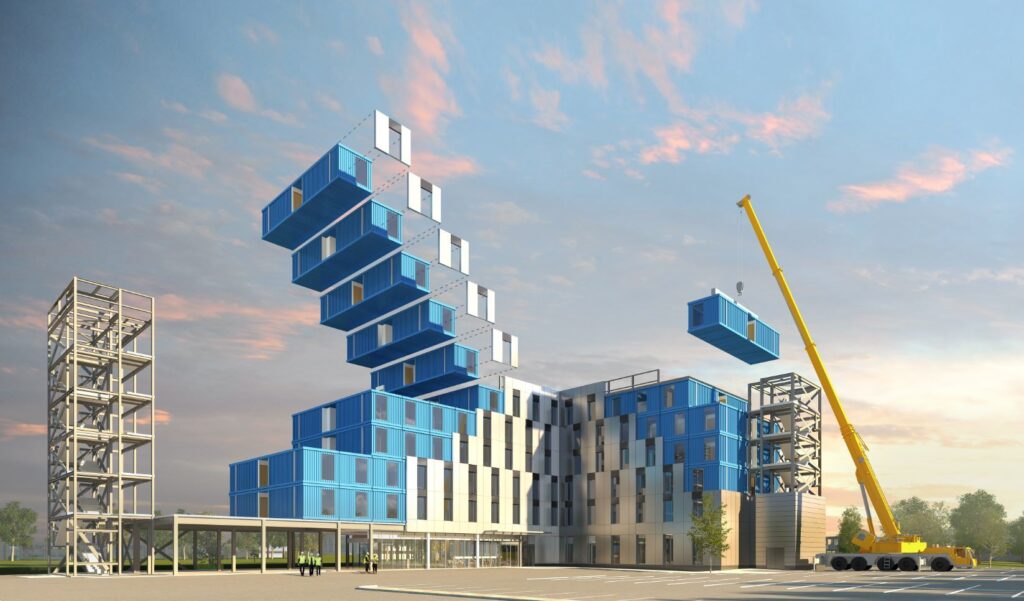
Now we’re going to delve into some history as we answer the question of when was it invented? The first recorded instance of modular construction came in the 1830s, when a London carpenter called John Manning made a prefabricated home for his son. This home was made in parts before being shipped from England to Australia where it was then reassembled. This construction method was also popular during the 1840s California Gold Rush in the United States, when it was used to build the ‘Crystal Palace for Britain’s Great Exhibition’ of 1851, and grew in popularity with the creation of prefab structures both during World War Two and for rapid rebuilding of homes following the end of the war.
Characteristics of modular construction
Factory-based manufacturing:
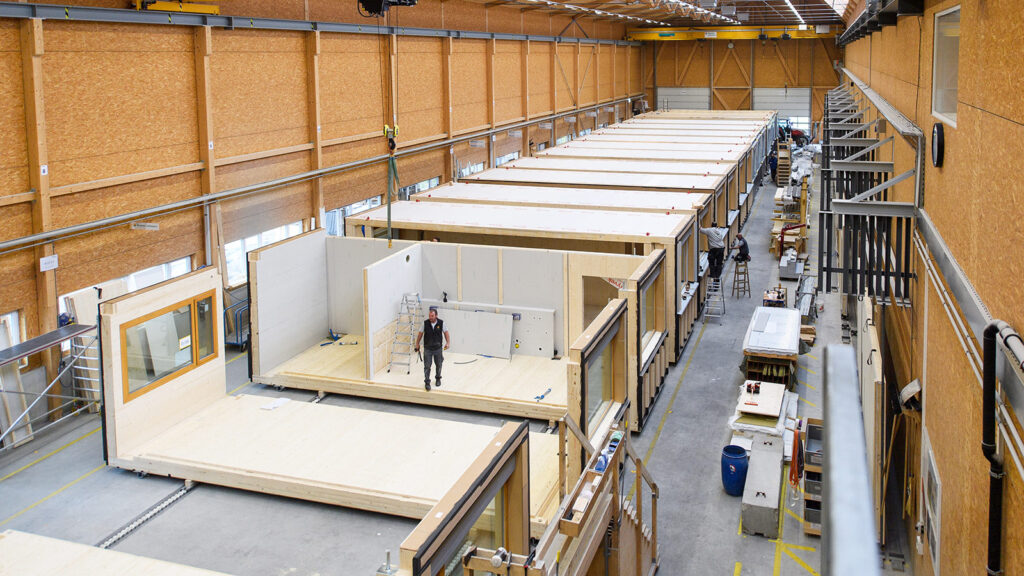
Modular construction involves the assembly of building components, such as walls, floors, and roof sections, in a factory rather than on the construction site. This controlled environment allows for higher precision and quality control.
Standardisation:
Modules are often designed to standard dimensions, which makes them easier to transport and assemble. This standardisation can also lead to cost savings and efficiency.
Speed of construction:
Modular construction is typically faster than traditional construction methods because many components are manufactured concurrently. This can significantly reduce project timelines, making it a preferred method for projects with tight schedules.
Reduced on-site disruption:
Since much of the construction work is completed in a factory, there is less on-site disruption, noise, and environmental impact. This can be advantageous in densely populated or sensitive areas.
Quality control:
Factory-based construction allows for strict quality control measures to be implemented, reducing the likelihood of errors and defects in the final product.
Cost-effectiveness:
While the initial manufacturing costs can be higher than traditional construction methods, modular construction can lead to cost savings in terms of labour, reduced construction time, and minimised waste.
Flexibility:
Modular construction is adaptable to various architectural styles and building types, from residential homes and commercial buildings to healthcare facilities and educational institutions.
Sustainability:
Modular construction is more environmentally friendly than traditional construction because it often generates less waste and reduces energy consumption during the construction phase.
Transportability:
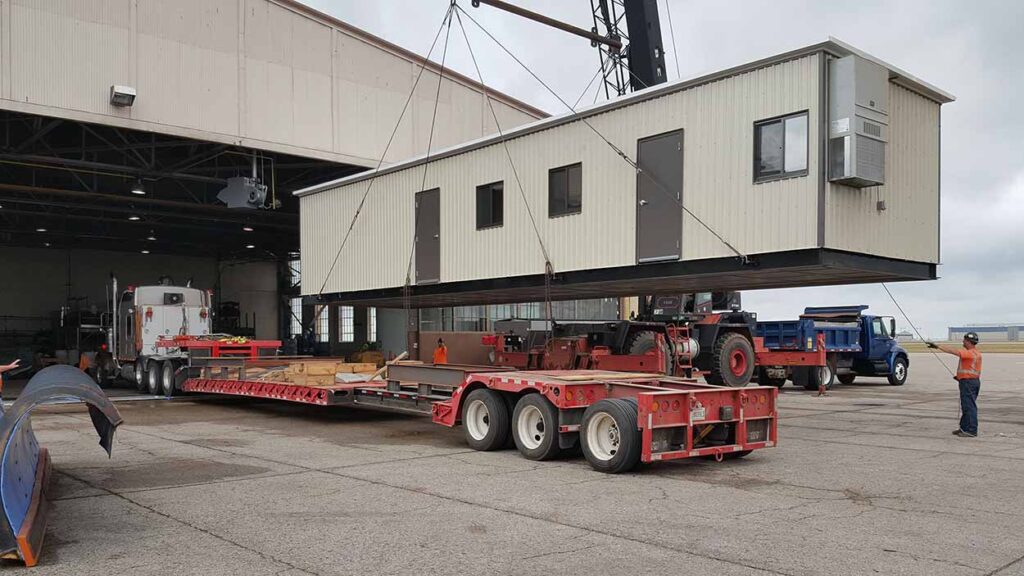
Modular components are designed to be transported to the construction site, making it feasible to construct buildings in remote or challenging locations.
Scalability:
Modular construction allows for easy expansion or modification of existing structures by adding or removing modules as needed.
Ultimately, this construction method has gained popularity in recent years due to its efficiency, quality control, sustainability advantages and especially due to the Mini Sky City construction. It will continue to evolve along with advancements in building technology and materials.
The Mini Sky City construction process
The construction of the Mini Sky City involved a well-coordinated series of steps and innovations, which had to have been expected, especially from a skyscraper constructed in merely 19 days. It was a highly coordinated effort that leveraged advanced construction techniques, prefabrication and modular construction principles in order to achieve the impressive speed and efficiency. And while this project gave a unique demonstration of rapid construction, it also sparked discussions in the construction industry about the potential for more efficient and sustainable building practices.
Design and planning phase:
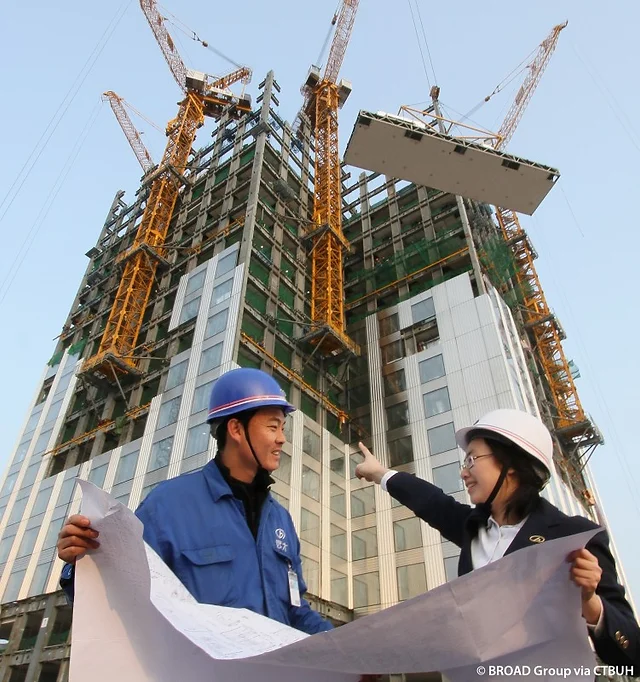
The project began with the conceptualisation of a skyscraper that could be constructed rapidly using modular construction techniques. Architects and engineers collaborated to design the building – incorporating modular elements and standardised components to streamline construction. Furthermore, while working on the blue prints and drawings, they were finding ways to make the layout of the building more efficient for such a fast way of construction.
The selection of materials – including types of steel, concrete, and other building materials – was crucial to ensure structural integrity while minimising weight and cost. Lastly, a factory environment for prefabrication was established near the construction site. This would soon reduce the cost of transport, as the prefabricated parts wouldn’t need to be transported over a long distance to reach the final construction site.
Prefabrication phase:
During the prefabrication phase, detailed designs for the prefabricated modules were created. These modules typically included walls, floors, and room sections with pre-installed plumbing, electrical, and HVAC systems. After the initial prototypes and test of materials, the factory then began manufacturing these modules on a larger scale. Precision machinery and skilled labour were employed to ensure the quality and consistency of each module. Rigorous quality control processes were implemented to inspect and verify the quality of each module. This step was critical to ensure that the modules would fit together seamlessly during assembly.
Transportation phase:
The prefabricated modules were transported to the construction site using specialised transport vehicles, such as flatbed trucks, and detailed logistics planning was also essential for an efficient transport. This involved route planning and scheduling to minimise delays. It was all made simpler as the modules were designed to be transportable without causing damage.
On-site assembly phase:
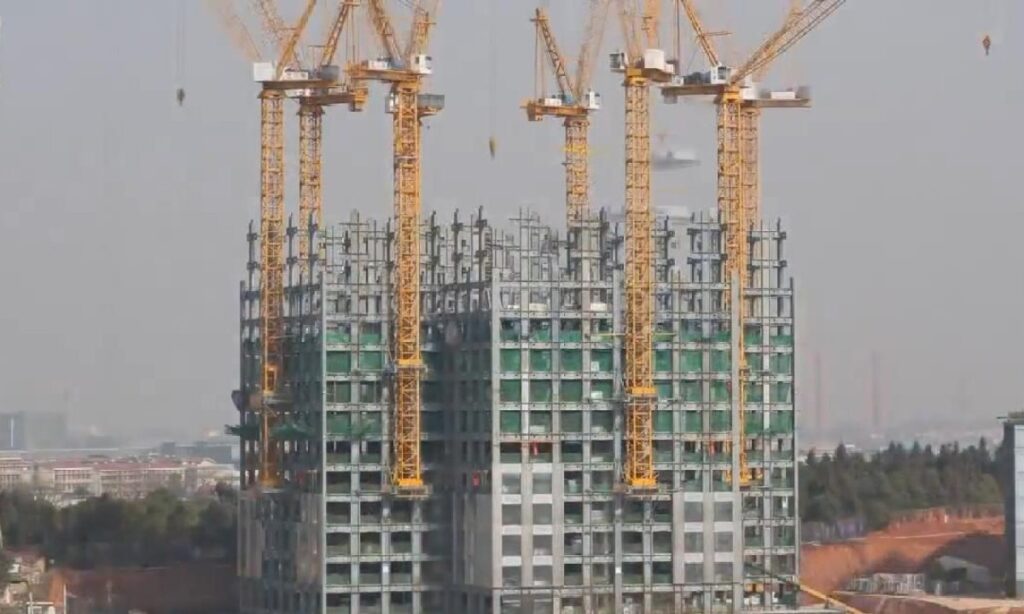
The construction site’s foundation and infrastructure, including utilities and support systems were all prepared in advance to the assembly. The modules were assembled in a predetermined sequence, with lower modules laid down first. Heavy lifting equipment and cranes were also used to position and secure each module in place. Furthermore, workers ensured that modules fit together seamlessly and securely – including all types of appliances that went between modules, such as plumbing, electrical and HVAC systems. Lastly, strict safety measures were enforced to protect the workers and ensure the stability of the building during construction.
Quality assurance and testing:
Continuous quality inspections were carried out during the assembly process to identify and rectify any issues promptly and efficiently. Safety and structural integrity are two of the most important aspects when it comes to building construction in general, therefore structural testing was taken very seriously in this project as well. Structural integrity tests were conducted to ensure the building’s stability and safety.
Finishing touches:
After the main structure was assembled, interior and exterior finishes, such as cladding, painting, flooring and fixtures were all installed. Moreover, comprehensive testing of all building systems, including electrical, plumbing, and HVAC, were performed to ensure they functioned correctly.
Final inspections and approval:
Lastly, the completed building underwent inspections made by relevant authorities to ensure compliance with safety and building codes. And finally, once all inspections were passed, the building received the necessary occupancy permit, therefore allowing people to move in.
Bibliography
- “China: Building a 57-Storey Skyscraper in 19 Days Thanks to HISTAR®.” Luxembourg.arcelormittal.com, https://luxembourg.arcelormittal.com/press/91/160/language/EN#:~:text=Customer%20Broad%20Sustainable%20Building%20recently.
- “Chinese Construction Firm Erects 57-Storey Skyscraper in 19 Days.” The Guardian, The Guardian, 30 Apr. 2015, www.theguardian.com/world/2015/apr/30/chinese-construction-firm-erects-57-storey-skyscraper-in-19-days.
- Press, Associated. “Chinese Builders Erect 57-Story Skyscraper in 19 Days.” New York Post, 30 Apr. 2015, https://nypost.com/2015/04/30/chinese-builders-erect-57-story-skyscraper-in-19-days/

